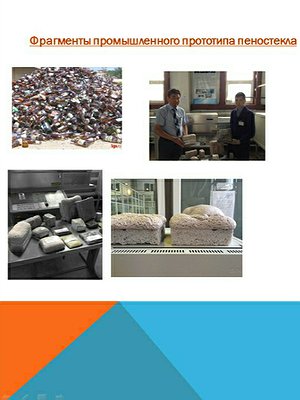
Автор: Бегеев Рустем
Научная работа
Объектом исследования является стеклобой, доменный и фосфорный гранулированный шлак, кремнистая порода–опока Таскалинского месторождения (ЗКО).
Цель проекта - Разработка технологических решений по переработке кремнезем и стеклосодержащего силикатного сырья Республики Казахстан. Исследование по выбору эффективного пенообразователя для получения пеностекла с требуемой микроструктурой. Разработка оптимального композиционного состава пеностекла. Разработка эффективных технологических режимов варки стекла, помола, обжига и вспенивания
По результатам проведенных работ выполнены следующие работы:
- изучены физико-механические и химико - минерологические сырьевых материалов, которые позволили определить и установить основные технологические решения для производства пеностекла;
- установлены, что крупнотоннажные стеклосодержащие отходы в виде доменного гранулированного и фосфорного шлака уникальные сырьевые материалы в качестве модифицирующих компонентов за счет содержания в них минералов волластонита. Применение этих сырьевых материалов в шихтовом составе для производства пеностекла обеспечивает конструкционные качества готового продукта;
- по результатам научно-экспериментальных исследований и с учетом микроструктуры лабораторных образцов установлено, что лучшие физико – механические технологические свойства с оптимально микроструктурой достигаются при использовании в качестве пенообразователя – мела;
- по результатам экспериментальных исследований определены влияние различных добавок на физико – механические свойства пеностекла при постоянном содержании пенообразователя;
- разработан наиболее эффективный режим обжига и вспенивания пеностекла.
ВВЕДЕНИЕ
Экологическое использование сырья в производстве энергозатратных строительных материалов, для потребителей сырьевых и энергетических ресурсов является актуальной задачей в условиях удорожания энергоносителей.
В этой связи все более ценным сырьем становятся отходы стекла - стеклобой, а также стеклосодержащие отходы, такие как доменные и фосфорные гранулированные шлаки, границы, применения которых с каждым годом расширяются благодаря научным работам зарубежных и отечественных специалистов.
В настоящее время они охватывают стекольную промышленность, дорожное строительство, промышленность строительных и теплоизоляционных материалов, композиционные материалы с использованием стеклобоя и стеклосодержащих отходов [1-11].
Стеклобой, как один из основных компонентов твердых отходов, негативно воздействует на окружающую среду в связи с выщелачиванием из него ряда веществ, оказывает травматологическое воздействие на организмы, невозможность разложения в естественных условиях.
В твердых бытовых отходах на долю стеклобоя приходится около 15 масс. %. При этом если принять, что в развитых странах на одного человека в год образуется 400-700 кг твердых бытовых отходов, то на одного человека образуется примерно 60-100 кг стеклобоя.
Ежегодно в крупных городах вывозится на захоронение 4-4,5 млн. тонн отходов, в которых примерно 600-700 тысяч тонн составляет стеклобой, а ежегодное количество последнего в западноевропейских странах оценивается в десятки миллионов тонн. Стекло невозможно окислить или разложить, количество стекла накопленного и продолжающего поступать в окружающую среду сопоставимо с природными геологическими ресурсами, используемыми человечеством.
С этой точки зрения стеклобой можно рассматривать как минеральный ресурс - аморфный силикатный материал антропогенного происхождения. Между тем, технология природных силикатных материалов ведет к значительным затратам материальных и энергетических ресурсов и неблагоприятному воздействию на окружающую среду как при добыче, так и при переработке полезных ископаемых. Тем не менее, антропогенный источник силикатных материалов - стеклобой - используется в крайне ограниченных количествах [12-18].
Утилизация или вторичное использования стеклобоя основаны на использовании его в качестве добавки к тем или иным технологическим процессам, при этом используются те свойства стекла, которые близки к свойствам заменяемого сырья.
Наиболее актуальным направлением использования стеклобоя является рассмотрение его не как добавки к существующим материалам, а как самостоятельного вида сырья. Такой подход позволяет не «подстраивать» существующие технологии под утилизацию отхода, а создавать новые технологии на основе комплексного исследования свойств сырья и получения качественных и востребованных материалов с комплексом заданных свойств [19-25].
Одной из основных задач проводимой реформы ЖКХ является снижение энергопотребления, что невозможно без внедрения в практику строительства и реконструкции эффективных теплоизоляционных материалов.
Подсчитано, что 1 м3 теплоизоляции обеспечивает экономию 1,4-1,6 тонн условного топлива в год. Именно по этому пути повышения эффективности работы ЖКХ пошли промышленно развитые страны. Так, например, объем выпуска теплоизоляционных материалов на 1000 жителей составляет в Швеции 600 США 500 м3, в Финляндии 420 м3, в то время как в России всего 90 м3 [19].
Между тем, одним из перспективных путей переработки боя стекла является производство строительного и теплоизоляционного материала - пеностекла. На сегодняшний день данное производство практически неразвито, а имеющееся используют специально сваренное стекло и сортированный стеклобой добавляют лишь в незначительных количествах. Кроме того, в технологии пеностекла не задействованы также крупнотоннажные стеклосодержащие отходы, такие как доменный и фосфорный гранулированные шлаки. Содержание стеклофазы в этих шлаках составляет до 95%.
Создание технологии получения пеностекла позволило бы увеличить объёмы производства теплоизоляционных материалов как минимум на 200 м3 на тысячу жителей.
Энергозатраты при производстве пенополистирольных материалов составляют 18900 кВт-ч/м3, минеральной ваты - 10000 кВт-ч/м3 [20]. В этом случае, о каком сокращении расходов энергии можно говорить, если изначально требуется затратить много энергии? Энергозатраты при производстве пеностекла в 30-60 раз ниже, чем при производстве пенополистирольных материалов и минеральной ваты.
В связи c этим создание эффективной технологии производства пеностекла из стеклобоя, кремнезем и стеклосодержащих отходов, таких как доменный и фосфорный гранулированные шлаки в полной мере учитывающей особенности его образования, состава и свойств, как самостоятельного сырья, является актуальной научно-практической задачей.
Отличительной особенностью предлагаемой нами технологии производства пеностекла являются:
- анализ природных и техногенных сырьевых ресурсов Республики Казахстан с целью получения пеностекла, отвечающего критериям энергоэффективности и рационального использования сырьевых ресурсов;
- разработка новых компонентных составов пеностекла отвечающего требованиям эффективной теплоизоляции и теплоизоляционно-конструкционных качеств;
- создание оптимальных технологических параметров производства пеностекла отвечающего требованиям технологической простоты на стадиях подготовки сырья и термообработки;
- создание промышленного прототипа пеностекла, используемого не только для теплоизоляции, но и в качестве ограждающих конструкций зданий и сооружений.
Научная новизна:
Предлагаемая технология отличается следующими новыми технологическими решениями:
- созданы новые компонентные составы отвечающие требованиям энергоэффективности и рационального использования природных и техногенных сырьевых ресурсов;
- разработаны новые технологические решения на стадии подготовки сырья, включающие совместный помол компонентов пеностекла в одном агрегате;
- разработаны новые технологические решения на стадии термообработки, включающие смещение температуру размягчения стеклопорошка в области низких температур;
- создан промышленный прототип пеностекла с волластонитовой структурой, который обеспечивает прочность при сжатии и изгибе с сохранением теплоизоляционных и конструкционных свойств;
- создан новый материал класса ЛЭЭНДТ (легкий, экономичный, экологичный, негорючий, долговечный, технологичный).
Цели исследования:
- разработка оптимальных составов сырьевых смесей для получения пеностекла требуемого качества на стадии подготовки сырьевых материалов;
- исследования влияния различных технологических факторов на физико-механические свойства пеностекла;
- разработка оптимальных технологических параметров для достижения высоких теплоизоляционных и прочностных характеристик готового продукта;
- разработка технологических режимов обжига в муфельной печи;
- разработка технологической схемы производства пеностекла на основе стеклобоя, кремнезем и стеклосодержащих отходов, таких как доменный и фосфорный гранулированные шлаки;
- создание промышленного прототипа отечественного пеностекла с волластонитовой структурой;
- проведение научно-экспериментальных работ по испытанию промышленного образца пеностекла в реальных конструкциях зданий и сооружений.
Решались следующие задачи:
- разработка технологических решений по переработке кремнезем и стеклосодержащего силикатного сырья Республики Казахстан;
- исследование по выбору эффективного пенообразователя для получения пеностекла с требуемой микроструктурой;
- разработка оптимального композиционного состава пеностекла;
- разработка эффективных технологических режимов варки стекла, помола, обжига и вспенивания.
ОСНОВНАЯ ЧАСТЬ
1 Методы испытаний и исследований
1.1 Аппараты, лабораторные оборудования
Для проведения научно – экспериментальных исследований по определению прочности при сжатие и изгибе образцов пеностекла, проводились на прессе ПГМ – 500 МГ4.
Для предварительного измельчения стеклобоя и кремнистой породы применяли щековую дробилку ДЩ 80-150.
Окончательный помол производился в лабораторной шаровой мельнице марки МШЛ 250х100.
Для определения морозостойкости образцов - пеностекла применяли камеру тепла и холода КТХ.
Сушка сырьевых материалов производилась в сушильном шкафу ШСП – 0,5 – 70 при t=900С и выдерживали до постоянной массы.
После помола стеклопорошки засыпались в формы в виде плит, балочек и блоков термообрабатывались в электрической печи СНОЛ 80/12 для вспенивания образцов.
Для получения гранулированного пеностекла стеклопорошки сначала гранулировались в грануляторе Т – 100 и термоообарабатывались для вспенивания в лабораторной высокотемпературной вращающейся печи RSR120/1000/13, исследуемая область температуры обжига 700-11000С.
Для определения теплопроводности образцов пеностекла использовали измеритель теплопроводности ИТП-МГ-4 «ЗОНД».
Для определения средней плотности, водопоглащения образцов пеностекла, для взвешивания сыпучих и кусковых материалов, использовали лабораторные весы.
1.2 Методика исследования химико-минералогических и физико-механических свойств образцов пеностекла
Тонкость помола контролировалась просеиванием через сито №0,063.
Формовка образцов произведена по методу полусухого формования.
Водопоглащение определяли по разности массы навески до и после насыщения ее водой. Насыщение водой производили в течение 1 ч, при уровне воды выше верха образцов не менее 2 см.
Измерение теплопроводности образцов пеностекла производилось с помощью измерителя теплопроводности ИТП-МГ-4 «ЗОНД».
Морозостойкость образцов производили по ГОСТ 9758-86.
Обжиг натурных изделий производились в электрических печах марок СНОЛ 80/12 и RSR120/1000/13.
2 Сырьевые материалы природного и техногенного происхождения
Кремнистая порода – опока
В качестве объекта исследования выбрана опока Таскалинского месторождения Западно-Казахстанской области.
Кремнистая порода опока Таскалинского месторождения расположенного в 1,7-2,8 км к Ю-В от ст. Шипово.
Запасы опок Таскалинского месторождения утверждены геологической разведкой (протокол № 4589 от 26.04.1985 г.) в следующих количествах по категориям (в тыс. т): А -4223, В-6545 и С-9651.
Полезная толща представлена тонкослоистыми, пористыми опоками светло-серого или серого цвета сызранского яруса нижнего палеогена. Мощность полезной толщи - 4,25-28,0 м, средняя - 19,1 м. Вскрытая мощность опок 49 м. Площадь распространения опок десятки кв. км. Вскрышные породы - супеси, суглинки, мощностью 0,2—6,0 м.
Были отобраны партии сырьевых материалов кремнистых пород, для проведения пробоподготовки для последующих экспериментальных исследований. В качестве кремнистой породы выбрана опока Таскалинского месторождения Западно-Казахстанской области.
Анализ выбранных опок показали, что они менее плотные, чем глинистая порода, их средняя плотность составляет 1,1-1,6 г/см3. Установлено, что опоки Таскалинского месторождения имеют в природном виде различные цвета: темно – серые, светло-серые и серые.
При добыче из карьера образуют камневидные валуны, размеры кусков валунов колеблется в пределах от 5 до 550мм. Встречаются в незначительном количестве пористые и слабые опоки. Экспериментально установлено, что естественная карьерная влажность опоки составляет 12-15%. По результатам поисковых исследований выявлено, что до настоящего времени опоки в качестве сырья для пеностекла практически не рассматривались. Хотя установленные данные и горнотехнические условия (большие мощности, выдержанный состав и многое другое) благоприятствуют о необходимости исследовательских работ по разработке технологии пеностекла.
3 Разработка технологических решений по переработке кремнезем и стеклосодержащего силикатного сырья Республики Казахстан
На начальном этапе исследования сырьевые материалы в виде стеклобоя, доменного и фосфорного гранулированных шлаков и кремнистой породы – опоки сушились в сушильном шкафу при температуре 90-95ОС до остаточной влажности 5-7%.
Стеклобой (тарное и оконное) и кремнистая порода – опока подвергались предварительному дроблению в лабораторной щековой дробилке до образования кусков 5 – 15мм для последующего помола в лабораторной шаровой мельнице.
В технологии пеностекла особое значение имеет удельная поверхность молотых порошков и температуры размягчения стеклофазы, поэтому нами проведены научно – исследовательские работы по установлению закономерности и зависимости температуры размягчения сырья по удельной поверхности. Ниже представлены результаты проведенных научно – экспериментальных исследований (таблица 5).
Таблица 5 - Зависимость от температуры размягчения сырья от удельной поверхности
Компонентный состав смеси |
Стадия подготовки |
Удельная поверхность, см2 /г |
Температура размягчения, 0 С |
Стеклобой |
Дробление и помол в шаровой мельнице |
1000-1200 1500-2000 2500-3000 3000-4000 |
850 860 780 740 |
Доменный гранулированный шлак |
Помол в шаровой мельнице |
1000-1200 1500-2000 2500-3000 3000-4000 |
900 880 850 760 |
Фосфорный гранулированный шлак |
Помол в шаровой мельнице |
1000-1200 1500-2000 2500-3000 3000-4000 |
850 830 800 750 |
Кремнистая порода – опоки |
Дробление и помол в шаровой мельнице |
1000-1200 1500-2000 2500-3000 3000-4000 |
1100 1050 1020 1000 |
Как показывают результаты научно - экспериментальных исследований, увеличение удельной поверхности снижают температуру размягчения сырьевых материалов. Самые благоприятные показатели температуры размягчения наблюдаются у стеклобоя и доменного и фосфорного гранулированного шлака.
Так температура размягчения стеклобоя при удельной поверхности 3000 - 4000 см2 /г, составляет 7400С. Следует отметить, что температура размягчения доменного и фосфорного гранулированного шлака при такой удельной поверхности находятся в пределах 750 - 7600С.
Следовательно, предоставляется возможность совместного использования их в производстве пеностекла композиционного состава.
Что касается кремнистой породы –опоки, то температура размягчения находиться в области высоких температур (1000–10200С), что указывает на необходимость проведения дополнительных исследований о разработке композиционного состава сырья с целью снижения температуры размягчения.
4 Исследование по выбору эффективного пенообразователя для получения пеностекла с требуемой микроструктурой
Одним из важнейших технологических решений для производства пеностекла является выбор эффективного пенообразователя. Для проведения экспериментов было выбрано 2 вида пенообразователя. В качестве первого пенообразователя был выбран мел месторождения «Меловые горки» г. Уральска. В качестве второго пенообразователя был выбран уголь Карагандинского месторождения.
Для получения материала с минимальной плотностью необходимо определить оптимальное количество пенообразователя. Для этого проводилась серия опытов с постоянным содержанием исходных компонентов, кроме мела, который в данном случае являлся пенообразователем.
На начальном этапе научно – экспериментальные работы проводились на основе стеклобоя без добавок. Все опыты проводились на 1 кг исходной смеси. Содержание мела в составе композиции варьировалась от 1 - 5 %. В качестве исследуемого свойства была выбрана средняя плотность вспененных образцов. Для проведения научно – экспериментальных работ стеклобой сначала дробили и загружали в шаровую мельницу. Мел дозировали в требуемом количестве и тоже загружали в шаровую мельницу. После этого производился совместный помол в шаровой мельнице до удельной поверхности 3000 см2 /г.
Удельную поверхность порошков контролировали путем просеивания через сито №0,063. Полученные порошки засыпали в металлические формы в виде плиты размером 100х100мм и толщиной 10 мм. После этого металлическая форма со стеклопорошком помещали в электрическую муфельную печь для последующей термообработки.
Термообработку производили по следующему режиму:
- нагрев осуществляли 7-12оС в минуту до 800-850оС,
- выдерживали при температуре 800-850оС в течение 1-1,5 ч и охлаждали в отключенной печи.
Полученные готовые образцы подвергались испытанию по определению средней плотности.
По результатам научно-экспериментальных исследований и с учетом микроструктуры лабораторных образцов установлено что лучшие физико – механические и технологические свойства с оптимально микроструктурой достигается при использовании в качестве пенообразователя мела (рисунок 23 и 24).
5 Разработка оптимального композиционного состава пеностекла
Наиболее перспективным направление исследования в технологии пеностекла является снижение энергозатрат и ресурсов путем вовлечения крупнотоннажных отходов как гранулированные доменные и фосфорные шлаки.
Кроме того, использование в качестве основного сырья кремнистых пород в виде опоки тоже является эффективным и перспективным направлением в совершенствовании энергосберегающих технологий. Данное направление должно основываться на результатах фундаментальных исследований физико-химических и химических процессов силикато - и стеклообразования процессов теплообмена в технологических агрегатах.
В связи с этим все более ценным сырьем становятся отходы стекла - стеклобой, применения которого расширяются благодаря научным работам. Основным барьером организации производства пеностекла в Казахстане, является отсутствие технологии для получения дешевого материала. Следующим этапом исследования является определение оптимального состава композиций для производства пеностекла.
Для достижения поставленных целей были составлены несколько шихтовых составов по композиционным системам порошок стеклобоя - доменный гранулированный шлак и стеклобой - фосфорный гранулированный шлак.
Проведение научно-экспериментальных работ осуществлялось в следующей последовательности: дробление стеклобоя, дозирование, загрузка сырьевых материалов в шаровую мельницу для проведения совместного помола, совместный помол композиций. Полученный композиционный стеклопорошок засыпался в жаростойкие металлические формы в виде плиты размером 100х100х10мм, плиты в виде балочек с размерами 160х40х40мм и в виде куба100х100х100мм, указанные размеры и формы образцов позволяют испытывать физико-механические свойства готовых образцов;
Обожженные и вспененные образцы пеностекла подвергались испытаниям по определению физико-механических свойств.
Результаты исследования влияния различных добавок на физико-механические свойства пеностекла приведены в таблице 6.
Таблица 6 - Результаты исследования влияния различных добавок на физико-механические свойства пеностекла
Составы сырьевой композиции для пеностекла |
Вид добавки, масса % |
Средняя плотность, кг/м3 |
Прочность, МПА |
|
при сжатии |
при изгибе |
|||
Стеклопорошок с удельной поверхностью 3500 см2 /г – 97%, мел - 3,0 % |
- |
400 |
6,3 |
0,7 |
Стеклопорошок с удельной поверхностью 3500 см2 /г - 96%, мел - 3,0 % |
Доменный гранулированный шлак - 1% |
400 |
10,2 |
1,6 |
Стеклопорошок с удельной поверхностью 3500 см2 /г - 96%, мел - 3,0 % |
Фосфорный гранулированный шлак - 1% |
410 |
10,8 |
1,9 |
Стеклопорошок с удельной поверхностью 3500 см2/г - 95%, мел - 3,0 % |
Доменный гранулированный шлак - 2% |
450 |
11,3 |
1,8 |
Стеклопорошок с удельной поверхностью 3500 см2/г - 95%, мел - 3,0 % |
Фосфорный гранулированный шлак - 2% |
460 |
12,2 |
1,97 |
Стеклопорошок с удельной поверхностью 3500 см2/г - 94%, мел - 3,0 % |
Доменный гранулированный шлак - 3% |
620 |
12,4 |
2,1 |
Стеклопорошок с удельной поверхностью 3500 см2/г - 94%, мел - 3,0 % |
Фосфорный гранулированный шлак - 3% |
640 |
13,1 |
2,6 |
Стеклопорошок с удельной поверхностью 3500 см2/г - 92%, мел - 3,0 % |
Доменный гранулированный шлак - 5% |
650 |
15,2 |
2,3 |
Стеклопорошок с удельной поверхностью 3500 см2/г - 92%, мел - 3,0 % |
Фосфорный гранулированный шлак - 5% |
670 |
16,1 |
2,7 |
По результатам научно - экспериментальных работ установлены основные закономерности изменения физико – механических свойств пеностекла при постоянном содержании пенообразователя.
В результате научно – экспериментальных работ выявлено, что добавление доменного и фосфорного гранулированного шлака ведет к стабильному росту прочностных показателей образцов – пеностекла по сравнению с образцами пеностекла на основе чистого стеклобоя. Добавление в состав стеклопорошка доменного и фосфорного гранулированного шлака в количестве от 1- 5 % повышает прочность при сжатии на 2,6 раз, а также наблюдается повышение плотности от 400 до 670 кг/м3. По полученным данным можно сделать вывод, что эти добавки эффективны касательно улучшения физико – механических свойств пеностекла при сохранении требуемой средней плотности и теплоизоляционных свойств. Поэтому составы №4 - 9, обеспечивающие низкие средние плотности пеностекла при сохранении высоких прочностных показателей, были выбраны в качестве наиболее эффективной и оптимальной композиции.
Определение коэффициента теплопроводности образцов пеностекла на приборе - измерителя теплопроводности ИТП-МГ-4 «ЗОНД». Результаты проведенных научно - экспериментальных работ приведены в таблице 7.
Таблица 7 - Результаты исследования влияния различных добавок на физико-механические свойства пеностекла
Составы сырьевой композиции для пеностекла |
Вид добавки, масса % |
Коэффициент теплопроводности, Вт/мхК |
|
Стеклопорошок с удельной поверхностью 3500 см2 /г – 97%, мел - 3,0 % |
- |
0,069 |
|
Стеклопорошок с удельной поверхностью 3500 см2 /г - 96%, мел - 3,0 % |
Доменный гранулированный шлак - 1% |
0,071 |
|
Стеклопорошок с удельной поверхностью 3500 см2 /г - 96%, мел - 3,0 % |
Фосфорный гранулированный шлак - 1% |
0,071 |
|
Стеклопорошок с удельной поверхностью 3500 см2/г - 95%, мел - 3,0 % |
Доменный гранулированный шлак - 2% |
0,073 |
|
Стеклопорошок с удельной поверхностью 3500 см2/г - 95%, мел - 3,0 % |
Фосфорный гранулированный шлак - 2% |
0,073 |
|
Стеклопорошок с удельной поверхностью 3500 см2/г - 94%, мел - 3,0 % |
Доменный гранулированный шлак - 3% |
0,074 |
|
Стеклопорошок с удельной поверхностью 3500 см2/г - 94%, мел - 3,0 % |
Фосфорный гранулированный шлак - 3% |
0,074 |
|
Стеклопорошок с удельной поверхностью 3500 см2/г - 92%, мел - 3,0 % |
Доменный гранулированный шлак - 5% |
0,075 |
|
Стеклопорошок с удельной поверхностью 3500 см2/г - 92%, мел - 3,0 % |
Фосфорный гранулированный шлак - 5% |
0,075 |
|
Результаты исследований определения коэффициента теплопроводности композиций пеностекла показали, что коэффициент теплопроводности почти не меняется с добавлением доменного и фосфорного гранулированного шлака. Данный коэффициент теплопроводности является очень хорошим показателем для теплоизоляционного материала пеностекла.
ЗАКЛЮЧЕНИЕ
1) Изучение физико-механических и химико-минерологических сырьевых материалов позволили определить и установить основные технологические решения для производства пеностекла:
- в качестве основного сырья наиболее приемлема кремнистая порода – опока и бой тарного, оконного и промышленного стекла;
- крупнотоннажные стеклосодержащие отходы в виде доменного гранулированного и фосфорного шлака уникальные сырьевые материалы в качестве модифицирующих компонентов за счет содержания в них минералов волластонита. Применение этих сырьевых материалов в шихтовом составе для производства пеностекла обеспечивает конструкционные качества готового продукта;
2) Для производства пеностекла с использованием исследуемых сырьевых материалов наиболее приемлемой стало следующее технологическое решение:
- первичное дробление сырьевых материалов;
- совместный помол сырьевых материалов до удельной поверхности 3000 – 5000 см2;
- засыпка готового порошка в формы в виде плиты и блока;
- вспенивание стеклопорошка в специальной печи при температуре 800- 9000С;
- резка готового продукта для придания стандартных форм изделий
3) По результатам научно-экспериментальных исследований и с учетом микроструктуры лабораторных образцов установлено что лучшие физико – механические си технологические свойства с оптимально микроструктурой достигается при использовании в качестве пенообразователя мела.
4) По результатам экспериментальных исследований определены влияние различных добавок на физико – механические свойства пеностекла при постоянном содержании пенообразователя. В качестве наиболее эффективной и оптимальной композиции был выбран составы №1-4, обеспечивающие низкие средние плотности пеностекла при сохранении высоких прочностных показателей;
5) На стадии подготовки сырьевых смесей определена требуемая удельная поверхность порошков по критерию минимальной температуры размягчения сырья;
6) Разработан наиболее эффективный режим обжига и вспенивания пеностекла. Установлено, что наиболее равномерная микроструктура пеностекла достигается при следующих режимах обжига: нагрев осуществляют со скоростью подъема температур 7-12оС в минуту до 900-950оС, выдерживают в течение 1-1,5 ч и охлаждают в печи.
СПИСОК ИСПОЛЬЗОВАННЫХ ИСТОЧНИКОВ
1 Дроздов В.А. Применение стекла в строительстве. -М.:Стройиздат. - 1983.-79 с.
2 Матвеев Г.М. Современные строительные материалы. Строительное и техническое стекло // Стекло и керамика.-1998.- №8.-С.6 -8.
3 Минько Н.И., Болотин В.Н., Жерновая Н.Ф. Технологические, энергетические и экологические аспекты сбора и использования стеклобоя (обзор)//Стекло мира.-1999.-№5.-С.3-5.
4 Гребцова В.Е. Экономическая и социальная география России.-Ростов-на-Дону: Феникс,1999.-285 с.
5 Китайгородский И.И. Технология стекла. - М.:Стройиздат, 1967.-490 с.
6 Дроздов В.А. Применение стекла в строительстве. - М.:Стройиздат, 1983.-79 с.
7 Кетов А.А. Пеностекло - незаслуженно забытый материал будущего Стекло и керамика.-2001.-№5.-С.5-7.
8 Саркисов П.Д., Овсяников Р.В., Спиридонов Ю.Л. Есть такой материал //СтройПРОФИль.-2002.-№4.–46с.
9 Нагибин Г.Е., Кирко В.И., Колосова М.М., Резинкина О.А., Мазалова А.А., Помилуйков О.В. Перспективы использования промышленных отходов в производстве изделий из пеностекла. Научно-исследовательский физико-технический институт КГУ.-2001.–120с.
10 Демидович Б.К. Пеностекло. - Минск: Наука и техника,1975.-248с.
11 Монтаев С.А. Разработка технологии производства теплоизоляционного материала - пеностекла./Монтаев С.А., Таскалиев А.Т., Жарылгапов С. М. // Евразийская интеграция: роль науки и образования в реализации инновационных программ: материалы международной научно – практической конференции. – Уральск,2012.-С.334-337.
12 Монтаев С.А. К вопросу теплоизоляции ограждающих конструкций зданий и сооружений пеностеклом / Монтаев С.А., Таскалиев А.Т., Жарылгапов С. М.//Архитектурно-строительное образование Казахстана: развитие и перспективы: сборник материалов международной научно-практической конференции. – Алматы,2011.-С.258-260.
13 Монтаев С.А. Технология пеностекла, модифицированного волластонитосодержащими сырьевыми материалами / Монтаев С.А., Таскалиев А.Т., Монтаева А. С.//Теория и практика повышения эффективности строительных материалов: сборник материалов VI международной конференции студентов, аспирантов и молодых ученых. – Пенза, 2011.-С.143-146.
14 Монтаев С.А. Создание энерго- и ресурсосберегающих технологий отечественного пеностекла / Монтаев С.А., Таскалиев А.Т., Монтаева А. С., Щучкин С.В. // Роль науки в реализации стратегии индустриально-инновационного развития Республики Казахстан: сборник материалов VIII международной научно-практической конференции молодых ученых и студентов. – Актобе, 2012.-С.357-359.
15 Монтаев С.А. Повышение энергоэффективности зданий и сооружений путем теплоизоляции наружних стен пеностеклом / Монтаев С.А., Таскалиев А.Т., Монтаева А. С.//Ауэзовские чтения-10: 20 –летний рубеж: инновационные направления развития науки, образования и культуры: сборник материалов междунар. науч-практ. конф. – Шымкент, 2011.-С.76-78.
16 Монтаев С.А. Пеностекло – эффективный теплоизоляционно – конструкционный материал для проектирования строительства энергоэффективных зданий и сооружений / Монтаев С.А., Таскалиев А.Т., Монтаева А. С.//Актуальные проблемы социально-экономического развития прикаспийского региона в условиях инновационной экономики: сборник материалов международной научно–практической конференции. – Элиста,2012.–С.95-97.
17 Пат. 26258 Республика Казахстан, Способ получения пеностекла/ Монтаев С.А., Таскалиев А.Т., Адилова Н.Б., Жарылгапов С.М., Монтаева А.С. Заявитель и патентообладатель Зап.-Каз.Аграр.-техн.ун-т.-№2011/1264.1; заявл.06.12.2011; опубл.15.10.2012, Бюл.№10–3с.
18 Орлов Д. JI. Пеностекло - эффективный теплоизоляционный материал//Стекло мира.-1999.-№4.-С.66-68.
19 Лудиков В.И. Какие утеплители нам предлагают//МОСТ.-1997.- № 12.–65 с.
20 Cocking R. The challenge for glass recycling // Sustainable Waste Management: Proceedings of the International Symposium. 9-11 September. - Dundee UK, 2003.-P.73-78.
21 Егоров К.И., Мамина H.A. Отходы стекла - экология, информация, бизнес//Строительные материалы.-1998.-№10.–33 с.
22 Glusing А. К., Conradt R. Dissolution kinetics of impurities in recycled cullet//Recycling and Reuse of glass Cullet: Proceedings of International Symposium. 19-20 March. - Dundee UK, 2001.-P.29-31.
23 Meyer C. Recycled glass - from waste material to valuable resource//Recycling and Reuse of glass Cullet: Proceedings of International Symposium. 19-20 March. - Dundee UK, 2001.-P.1-10.
24 Пузанов А. И. Утилизация стеклобоя путем получения пеносиликатного теплоизоляционного материала:/Пермский государственный технический университет. – Пермь, 2004.–176 с